Introduction
Surfactants, also called surface-active agents, may act as detergents, foaming agents, wetting agents, dispersants and emulsifiers. They are the major components in household detergents, such as laundry detergents, home cleaning supplies, and personal toiletries (Yuan et al., 2014). Also, they are widely used in dishwashing detergents. Due to insufficient flushing water or rinse time during dishwashing, residual levels of surfactants are often found on the surfaces of dishware and may pose health risks (Zhao et al., 2017). Detergents have been shown to induce endocrine disorders upon interaction with estrogen receptor protein (Ying, 2006).
The US ANSI/NSF 3 and German DIN 10512 are the most popular standards for commercial dishwashers to improve hygiene (Wernersson et al., 2004). To fulfill ANSI/NSF standard, the removal of all visible soil and detergent from utensils is required. However, it is difficult to check the completeness of cleaning continuously. Therefore, utensils or dishware are often cleaned using excessive washing agent or rinsing agent, thereby wasting water resources and generating excessive wastewater. As a remedy, oxidizing agents such as ozone, ultraviolet radiation and nonthermal plasma could be applied at post-rinse stage of dishwashing to eliminate residual surfactants or other components of detergents from the surface of dishware since advanced oxidation processes (AOPs) generate hydroxyl radicals in sufficient quantities to be able to oxidize majority of complex chemicals (Aonyas, 2016).
In recent years, non-thermal plasma (NTP)-based AOPs have received increased attention. This is particularly due to the fact that NTPs generate various reactive oxygen species (ROS) and reactive nitrogen species (RNS) such as OH, H, HO2, O3 and NO, ONOO−, NO2−, NO3−, respectively; which possess high oxidation potentials to react with organic molecules (Attri et al., 2016). In a study, two types of atmospheric pressure plasma jets (APPJs) operating in Ar gas, a direct (D-APPJ) and an indirect (ID-APPJ), have been successfully applied to the degradation of methylene blue, methyl orange and Congo red dyes (Attri et al., 2016). The potential of a novel plasma-based AOP for efficient and cost-effective destruction of organic contaminants has been shown (Even-Ezra et al., 2009). In that study, tested Hydro- Non-Thermal-Plasma AOP system, which emits corona discharge, successfully destroyed trichloroethylene, 1,4- dioxane and N-nitrosodimethylamine with high levels of removal efficiencies of 95.3%, 91.7%, and 95.3%, respectively. Recently, a gliding arc plasma was used to degrade sodium laurylsulphate (NaLS) in a circulating reactor; about 90% degradation was noted after 500 min plasma treatment (Brisset et al., 2016).
Dodecylbenzene sulfonate-sodium salt (DBS) is an important anionic surfactant and is the predominant constituent of linear alkylbenzene sulfonate-sodium salt (LAS), the most commonly used active surfactant for dishwashing detergents worldwide (de Almeida et al., 1994). Residues of these surfactants on the surface of dishware after rinsing could be degraded using oxidants like NTPs. Therefore, in the present study, the effectiveness of dielectric barrier discharge (DBD) plasma was tested for the oxidative degradation of DBS and LAS surfactants. In addition, the degradation of DBS as a component of dishwashing detergents by DBD plasma was studied.
Materials and methods
Dodecylbenzene sulfonate-sodium salt (DBS) was purchased from Sigma-Aldrich Co. (St. Louis, MO, USA). Linear alkylbenzene sulfonic acid (LAS, Molecular formula- C18H30O3S, Purity-97%) was purchased from Alfa Aesar (Ward Hill, MA, USA). Dishwashing detergents, namely Product J (contained 9.11% DBS, w/w), Product S (contained 9.76% DBS, w/w) and Product P (contained 11.48% DBS, w/w) were purchased from a local supermarket. All other chemicals used were of analytical grade quality.
A custom-built DBD plasma generator was used in this study. Dimensions and operating conditions of the instrument were similar to those given in our earlier work (Puligundla et al., 2016). Briefly, a high-voltage (10 kV), pulsed DC power (frequency range of 10-50 kHz) was supplied as input power to plasma generating electrode. The plasma electrode measured 15 cm in length and 2 cm in width. Power consumption during plasma emission was 208 W. An aluminum plate was used as both sample stand and ground electrode. An aluminum oxide ceramic plate having a thickness of 0.65 cm acted as dielectric barrier material between the electrodes. An inter-electrode distance of 2.65 mm was maintained. DBD was generated in air at atmospheric pressure.
Test samples containing surfactants (DBS and LAS, 3%, w/w) and detergents (Product J, Product S and Product P, 10% w/w) in distilled water were prepared, respectively. Drops of the samples were taken onto glass slides (76×26 mm) (10 μL on each slide) spread and dried under a laminar air flow for 1 h. Thereafter, the slides were individually placed on the sample treatment plate and treated using DBDP generated under different plasma currents (2.0, 2.5, and 3.0 A) and at different inter-electrode gaps (2.0, 2.5, and 3.0 mm) for predetermined durations (0-120 min). Immediately after treatment, remaining surfactant or detergent levels from the glass surfaces were recovered using distilled water (100 mL for each slide) and quantified according to a spectrophotometric method using methylene blue (Ministry of Environment, 2011).
A 100 mL of simulated residual surfactant or dishwashing detergent sample, 5 mL of methylene blue (MB) solution and 10 mL of phosphate buffer (pH 10.0) were taken into a separatory funnel, and added 15 mL of 100% chloroform to it. The whole mixture was shaken vigorously for 1 min, and then allowed to separate into two distinct layers. Thereafter, bottom layer was collected and transferred into another (2nd) separatory funnel. Chloroform (15 mL) was again added to 1st funnel and repeated the steps to collect bottom layer into 2nd funnel. Later, into the 2nd funnel collection, acidic MB solution (5 mL) and deionized water (100 mL) were added, mixed well, and collected the bottom layer in a 50 mL volumetric flask via filtration (glass microfiber filter). Into the remaining content in the 2nd funnel, 5 mL of 100% chloroform was added, shaken and collected the bottom layer into the volumetric flask after filtration. This step was repeated once again. Finally, the collected content of the volumetric flask (50 mL) was used for quantification of residual surfactant using a spectrophotometer at 652 nm.
Surfactants degradation levels were calculated using the following equation:
where Ct was the concentration of surfactant or detergent at time (t), and C0 was the initial concentration of surfactant or detergent.
For modeling the degradation kinetics of the residual surfactants or surfactant in detergents, log-linear first-order kinetics models were used initially. Later, the appropriateness of other models including log-linear tail and Weibull was tested and compared with the log-linear model.
Log-linear model (Bigelow and Esty, 1920):
Log-linear tail model (Geeraerd et al., 2000):
Weibull model (Mafart et al., 2002):
where,
Results and Discussion
The inter-electrode gap between the plasma electrodes influenced the degradation of tested surfactants or surfactant in detergents on glass slides. An increase of the gap linearly decreased the efficiency of degradation. At all tested interelectrode gaps (2.0, 2.5, and 3.0 mm), an increase of input current (2.0, 2.5, and 3.0 A) increased the efficiency of degradation for all tested surfactants or detergents. In the case of DBS surfactant, a steep reduction by up to 50% of initial DBS concentration was observed upon DBDP (generated using current of 3.0 A) treatment within 15-20 min, at all tested inter-electrode gaps (Fig. 1). Thereafter, the rate of degradation was relatively slowed, ≥70% degradation was noted within 120 min of DBDP treatment at 2.0 mm interelectrode gap. At 2.5 mm inter-electrode gap, the levels of remaining DBS concentration on glass slides following DBDP treatment (for 120 min) at 2.0, 2.5, and 3.0 A were 54.54%, 50.25%, and 38.37% (of initial concentration), respectively. At 3.0 mm gap, remaining DBS levels after 120 min treatment were 62.35%, 52.44%, and 44.48% using DBDP at 2.0, 2.5, and 3.0 A current, respectively.
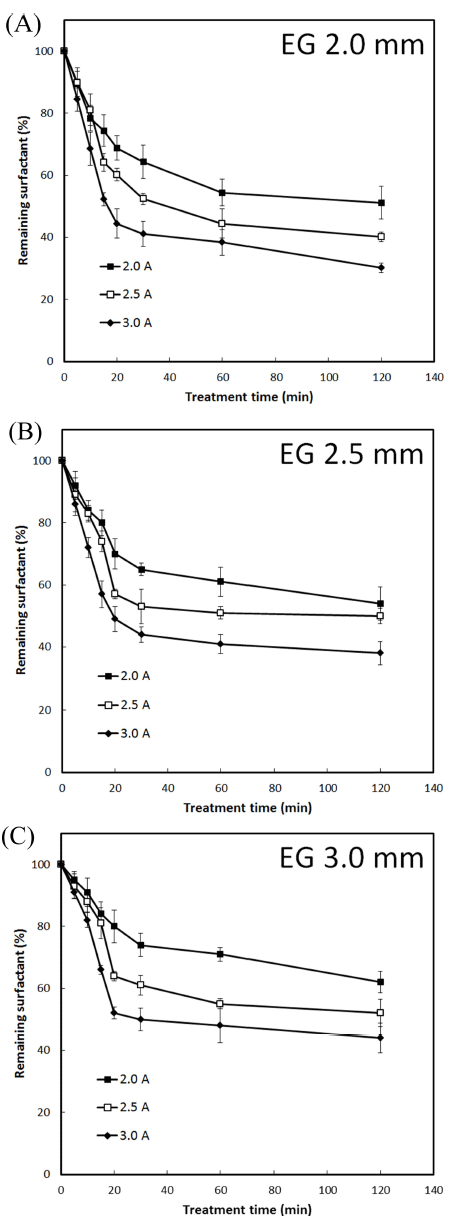
Similar degradation patterns were observed in the case of LAS surfactant upon DBDP exposure (Fig. 2). The levels of remaining LAS concentration following DBDP treatment (generated at 3.0 A current and treatment time of 120 min) at inter-electrode gap of 2.0, 2.5, and 3.0 mm were 32.38%, 42.46%, and 54.25%, respectively. At the other current levels tested, the efficiency of LAS degradation was relatively low (Fig. 2). On the other hand, in the case of Product J, Product S and Product P, % remaining surfactant in detergents after DBDP treatment (generated at 3.0 A current and treatment time of 120 min) at inter-electrode gap of 2.0 mm was 37.44, 39.49, and 34.41, respectively (Fig. 3).
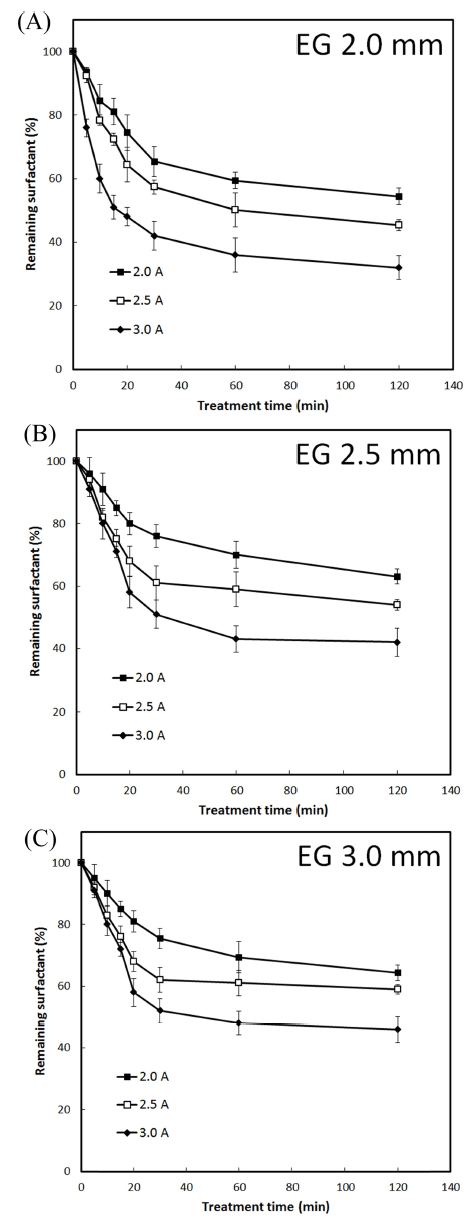
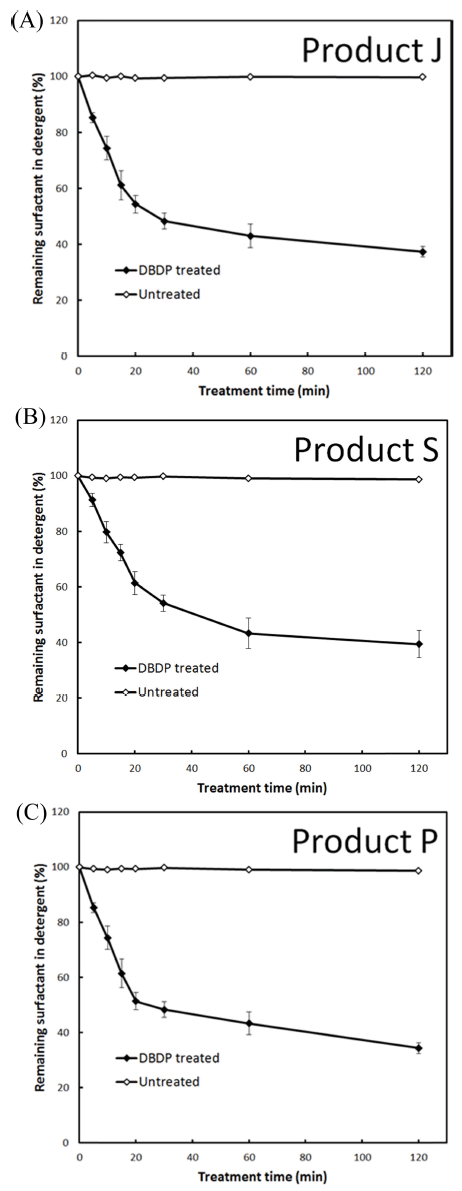
These results indicated that the initial concentrations of DBS and LAS surfactants on glass slides can be degraded up to 70% using DBDP generated with 3.0 A current, at 2.0 mm inter-electrode gap and a treatment time of 120 min. Under these conditions, surfactant in tested detergents was degraded by 60-65%.
Recently, DBD with falling liquid film has been shown to be effective for the degradation of two anionic surfactants (sodium lauryl sulfate–SDS and sodium dodecylbenzenesulfonate– SDBS). Results of that study showed that both surfactants (initial concentration of 100 mg/L) exhibited similar degradation trends and degradation efficiencies were nearly 90% (Aonyas et al., 2016).
To explain kinetically DBDP treatment-induced surfactant (DBS and LAS) degradation, the applicability of selected models, namely log-linear, log-linear tail and Weibull, was tested. Among these models, Weibull model was found to be best fit. The Weibull model fitted well with the degradation data as evidenced from the values of SSE (sum of squared errors) RMSE (root mean squared error), r2 (coefficient of determination or fit index). Relatively low SSE and RMSE values and a high r2 value (close to 1) for the Weibull model indicated that it was the best-fitting model compared with others (Table 1).
![]() |
The same Weibull model was used to explain surfactant (DBS and LAS) degradation at different process variables. As shown in Table 2, relatively low δ value (time to the first decimal reduction) values were observed for both DBS and LAS degradation using DBDP generated at 3.0 A current and 2.0 mm inter-electrode gap.
![]() |
Similar degradation patterns were observed for the degradation of NaLS by gliding arc electrical discharge (Brisset et al., 2016). In that study, two successive kinetic laws were noted; a pseudo zero order law was observed during initial stages of degradation and a pseudo first order decay was noted after a certain exposure period.
For wastewater treatment, electric discharge plasmas including DBDs are widely employed as AOPs. AOPs generate hydroxyl radicals (·OH), a strong oxidant, which can swiftly oxidize different organic compounds in wastewater (Cao et al., 2018). The hydroxyl radical could attack aliphatic part and/or aromatic ring of a molecule (Aonyas et al., 2016). When gas phase DBD plasma is used for wastewater treatment, the generation of ozone (O3) in the gas phase initially and followed by diffusion into the liquid phase has been shown. In the generation of ·OH in the liquid phase, the interactions of high-energy electrons with water molecules at the liquid-gas interface play crucial roles in addition to reciprocal reactions ·O with water molecules (Cao et al., 2018), as shown hereunder:
where * indicates a high-energy electron state.
In the generation of H2O2 in the liquid phase, the recombination of ·OH plays a significant role. Both physical (including shock waves, ultraviolet (UV) radiation and cavitation effects) and chemical effects (reactive species formation followed by oxidation of organic pollutants) play crucial roles in the degradation of organic contaminants (Cao et al., 2018).
Summary
Conditions for the oxidative degradation of simulated residual DBS and LAS surfactants as well as DBS surfactant in detergents by DBD plasma were optimized. Under the optimal degradation conditions, the initial concentrations of DBS and LAS on glass slides were decreased up to 70% in 120 min. Under the same treatment conditions, the initial levels of DBS in tested detergents were degraded up to 60- 65%. The Weibull model was found to be best-fit model compared with others to explain kinetics of degradation of the surfactants (both in pure form and in detergent formulation) by the plasma. As gas plasmas are known to produce different reactive species, radical reactions or oxidation by radical mechanisms might have played a dominant role in the abatement of the surfactants. In conclusion, it is an easily applicable approach to degrade residual surfactants on dishware in real-world settings.