서 론
우리나라는 지난 20년간 쌀 관세화를 유예한 대가로 연 간 408,700 ton의 쌀을 의무적으로 수입하고 있는 실정이 다. 이와 같은 상황은 국내 쌀 시장에 위협적인 요소이며, 국내 쌀 시장에 큰 위협요소가 될 것으로 예상된다.
쌀 시장 개방에 대응하기 위한 정부 정책은 고품질 쌀 생산체계로 전환되었고(Lee et al., 2013), 최근 미곡종합처 리장을 중심으로 안전한 고품질 쌀 생산, 생산비용절감 및 브랜드 파워 확대를 통한 경쟁력 강화를 목적으로 고품질 쌀 유통 활성화 사업이 진행되고 있다(Kang et al., 2015).
미곡종합처리장은 1991년부터 보급되기 시작하였으며, 수확 후 처리 비용 및 노동력 절감, 품질향상, 유통개선 등을 목적으로 설치된 농촌의 농업기반 및 쌀 유통의 중심 시설이다(Yoon, 2007). 기존 미곡종합처리장에서 사용되는 정백시스템은 연삭식 정미기, 마찰식 정미기, 연미기로 구 성되어 있기 때문에 에너지소비량이 많이 소요된다. 따라 서 국내산 쌀의 경쟁력 강화를 위한 생산단가 절감 방안으 로 정백시스템의 단위기계를 최소화하여 시설비용과 에너 지소비량을 절감할 필요가 있다. 또한 정백 중 곡온 상승 을 방지하여 도정수율 및 품질을 향상시킬 수 있는 새로운 정미기 개발이 필요하다.
정미기에 관한 연구개발은 초경날식 절삭형 완패스정미 기의 개발(Chung, 1997), 입형 배아미 생산시스템 개발에 관한 연구(Yan & Chung, 2004; Lim et al., 2014), 정백공정 중 연삭공정이 쌀 품질에 미치는 영향(Kang et al., 2010), 마찰과 연삭 도정배분의 따른 성능평가(Kim et al., 2009) 등을 수행하였으나, 절삭력을 이용한 정미기에 관한 연구 는 미진한 실정이다.
한편, 절삭력을 이용한 정미기는 비교적 낮은 정백압력 에서 현미의 호분층 제거가 가능하기 때문에 정백 시 에너 지소비량이 절감되고, 곡온 상승 및 싸라기율이 낮아 고품 질 백미 생산이 가능할 것으로 판단된다(Keum, 2008).
따라서 본 연구에서는 절삭식 정미기의 정백실 내부 흡 인 송풍량에 영향을 미치는 절삭롤러 통풍구 수와 현미 가공 중 발생하는 미강 제거에 필요한 송풍속도가 정백특 성에 미치는 영향을 구명하여, 기존의 정백시스템을 대체 할 수 있는 절삭식 정미기 개발의 기초자료를 제시하고자 한다.
재료 및 방법
Fig. 1은 본 연구에서 사용된 절삭식 정미기의 개략도를 나타낸 것이다.
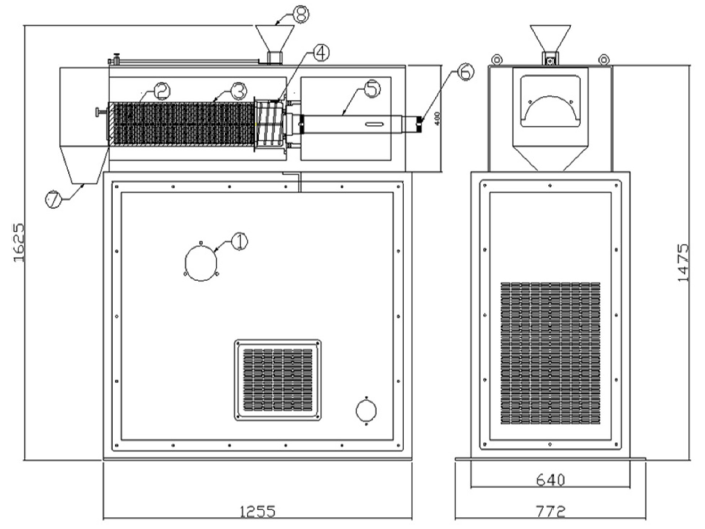
Fig. 1에서 보는 바와 같이 절삭식 정미기는 가로×세로 높이가 1,255×772×1,625 mm이며, 구성요소로는 절삭롤러, 금망, 이송스크루, 주축 등으로 이루어져 있다. 현미 투입 부에서 공급된 현미는 이송스크루를 통해서 정백실로 이송 된다. 또한 정백실은 주축에 절삭날 및 통풍간극링을 조립 한 절삭롤러와 금망으로 이루어져 있고, 정백 중 발생하는 미강을 흡인 팬에 의하여 제거한다.
통풍 간극링은 절삭식 정미기 주축으로부터 흡인된 공기 를 정백실로 공급하는 장치로 재질은 SS400강으로 제작하 였고, 레이저 가공 후 침탄 열처리를 통하여 내마모성을 증대시켰다. 본 연구에서는 정미기 주축으로부터 흡인된 공 기를 정백실 내부로 공급할 경우 적정 송풍량을 선정하기 위해 통풍 간극링의 통풍구 수를 2, 3, 4구로 나누어 제작 하였다.
통풍구 2구는 180° 간격으로, 통풍구 3구와 4구의 경우 각각 120°, 90° 간격으로 제작하였다.
절삭식 정미기의 정백특성을 분석하기 위한 공시재료는 충청북도 청주시 청원구 내수읍에서 생산된 2014년산 추청 현미를 사용하였다. 1회 시료량은 500 kg이었으며, 절삭롤러 길이는 570 mm, 축 직경 150 mm, 주축 회전속도는 1,000 rpm으로 하였다. 또한 시간당 생산량은 2 ton, 백도는 38± 0.5로 조절한 후 절삭롤러 통풍구 수 2, 3, 4구 및 송풍속도 30, 35, 40 m/s 조건에서 정백특성을 분석하였다.
곡온은 디지털 온도계(TES-1300, TES, Taipei, Taiwan) 를 이용하여 측정하였다. 정백 전 원료 현미의 곡온은 정 미기의 현미투입구에 온도계를 설치하여 측정하였고, 정백 후 백미의 곡온은 백미 배출구에 온도계를 설치하여 측정 한 최대온도로 나타내었다.
동할미율은 원료 현미의 동할미율과 정백 후 가공된 백 미의 동할미율을 측정하여 정백 전후 동할미율 차로 나타 내었다. 동할미율은 1회에 완전미 50립을 동할미투시기 (RC-50, Kett, Tokyo, Japan)를 이용하여 측정하였고, 10회 반복 측정하여 평균값으로 나타내었다.
싸라기율은 강선 지름 0.5mm, 10mesh의 진동선별기(HS- 6000, Hwasan, Gyeongsan, Korea)로 선별한 싸라기율과 가공된 백미 중 1 kg을 체눈 1.7 mm 진동체선별기(25M, Ooya, Tokyo, Japan)로 5분간 선별한 싸라기를 백미 1 kg에 대한 무게비로 산출한 싸라기율과 합산하여 나타내었다.
백미의 탁도는 백미 5 g 및 수온 20°C의 정수 400 mL를 비커에 넣고, 교반기(KA11-98, Kastech, Seoul, Korea)를 이용하여 30초간 진탕(진폭 40 mm, 1분 150회)한 용액을 수질측정기(90-FLT, TPS, Los Angeles, CA, U.S.A)로 3회 측정한 후 평균값으로 나타내었다(KFRI, 2010).
결과 및 고찰
Fig. 2는 절삭식 정미기의 절삭롤러 간극링의 통풍구 수 와 송풍속도 변화에 따른 정백 후 백도를 비교하여 나타낸 것이다.
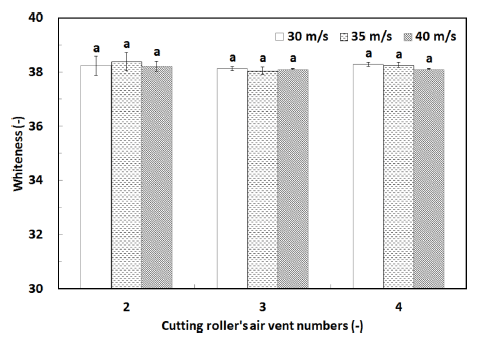
Fig. 2에서 보는 바와 같이 백도는 모든 조건에서 38± 0.5로 측정되어 정백 중 백도조절이 일정한 것으로 나타났 다. 정백 후 백미의 백도는 절삭롤러 통풍구 수에 따라 2 구의 경우 송풍속도 30, 35, 40 m/s 조건에서 각각 38.23, 38.38, 38.22로 나타났다. 또한 3구에서는 송풍속도 30 m/s 에서 38.13, 35 m/s는 38.05, 40 m/s에서는 38.11로 나타났 다. 또한 4구 조건의 경우 송풍속도 30, 35, 40 m/s에 따라 각각 38.29, 38.26 및 38.10의 백도 값을 나타내었다.
이와 같이 정백 후 백도 값이 큰 차이가 없는 것은 정 백 중 정백실 내의 압력이 일정하여 정백이 균일하게 이루 어졌기 때문으로 판단된다.
Fig. 3에 절삭식 정미기의 절삭롤러에 장착된 통풍 간극 링의 통풍구 수와 송풍속도 변화에 따른 정백 후 곡온 상 승을 나타내었다.
일반적으로 정백 후 곡온 상승 범위는 정백 전보다 15°C 이상 상승되지 않는 것이 바람직하다고 보고되고 있다. 또 한 곡온 상승이 높아지면 싸라기와 동할미율이 증가하고 수분손실이 많아져 품질이 저하된다(Keum, 2008).
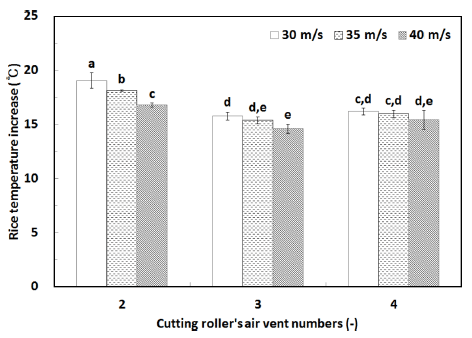
Fig. 3에서 나타냈듯이 정백 후 곡온 상승은 절삭롤러 통풍 간극링의 통풍구 수 2구의 경우 송풍속도 30, 35, 40 m/s 조건에서 각각 19.1, 18.1, 16.8°C로 나타났다. 또한 3 구에서는 송풍속도 30 m/s에서 15.8°C, 35 m/s는 15.4°C, 40 m/s에서는 14.6°C로 나타났다. 4구의 조건에서는 송풍속 도 30, 35, 40 m/s에 따라 각각 16.2, 16.0, 15.4°C로 나타 났다.
이와 같이 정백 후 백미의 곡온 상승은 송풍속도가 증가 할수록 낮아지는 경향을 보였으며, 절삭롤러 통풍구 수 3 구, 송풍속도 35, 40 m/s 조건에서 곡온 상승이 다른 조건 과 비교하여 약간 낮은 경향을 나타내었다. 또한 절삭롤러 통풍구 수 4구 조건이 3구 조건과 비교하여 곡온 상승이 약간 높은 이유는 4구의 경우 정백실로 공급되는 송풍량이 많아 정백 중 압력이 감소하여 백미의 백도를 높이기 위해 압력판의 압력을 가하였기 때문으로 판단된다.
한편, 정백 중 백미의 곡온 상승은 외기온도의 영향을 많이 받으며, 실험 중 외기온도가 29-32°C 정도로 높았던 것을 감안하면 통풍구 수 3구 및 4구 조건은 적정 곡온 상승 범위인 15°C와 비교하여 큰 차이가 없는 것으로 사 료된다.
Fig. 4에 절삭식 정미기의 절삭롤러 통풍 간극링의 통풍 구 수와 송풍속도에 따른 정백 전후 동할미율 차를 나타내 었다.
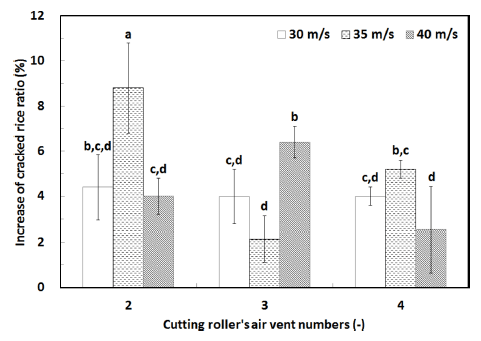
Fig. 4에서 알 수 있듯이 동할미율은 절삭롤러 통풍구 수 2구의 경우 송풍속도 30, 35, 40 m/s 조건일 때 각각 4.4, 8.8, 4.0%로 나타났다. 또한 3구에서는 송풍속도 30 m/s에서 4.0%이었으며, 35 m/s는 2.1%, 40 m/s에서는 6.4% 로 나타났다. 4구 조건의 경우 동할미율은 송풍속도 30, 35, 40 m/s에 따라 각각 4.0, 5.2, 2.5%로 나타나, 동할미율 이 가장 낮은 조건은 절삭롤러 통풍구 수 3구의 송풍속도 35 m/s 조건과 통풍구 수 4구의 송풍속도 40 m/s 조건에서 각각 2.1, 2.5%로 나타났다.
이와 같이 통풍구 수 3, 4구 조건이 2구 조건과 비교하 여 동할미율이 낮은 것은 2구에 비해 정백실로 이송되는 송풍량이 많아 마찰열이 감소하여 정백 중 곡온 상승이 낮 았기 때문으로 판단된다. 또한 통풍구 수 3구와 4구간에 동할미율 차이가 크지 않은 이유는 전술한 바와 같이 정백 중 곡온 상승이 비슷하였기 때문에 동할미 발생율 또한 차 이가 적은 것으로 판단된다.
Fig. 5는 절삭식 정미기의 절삭롤러 통풍구 수와 송풍속 도에 따른 정백 후 싸라기율 변화를 분석한 결과를 나타낸 것이다.
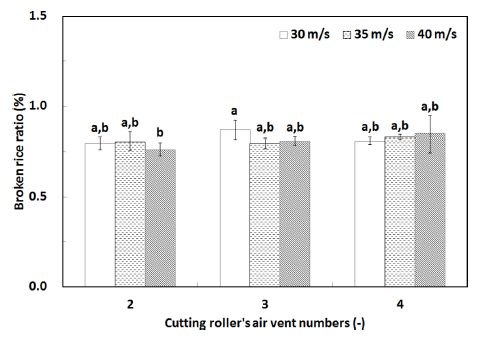
Fig. 5에 나타냈듯이 싸라기율은 절삭롤러 통풍구 수 2 구의 경우 송풍속도 30, 35, 40 m/s 조건에서 각각 0.796, 0.806, 0.762%로 나타났다. 또한 통풍구 수 3구와 4구인 경우 송풍속도에 따른 싸라기율 발생 범위는 각각 0.796- 0.869%, 0.809-0.847%로 싸라기율은 절삭롤러 통풍구 수 2구 송풍속도 40 m/s에서 0.762%로 약간 낮게 측정되었다.
본 연구에 사용된 절삭식 정미기의 싸라기율은 모든 조 건에서 0.762-0.869%로 낮은 범위를 나타내었으며, 통계분 석 결과 P 값이 0.05 이상으로 나타나 절삭롤러 통풍구 수 와 송풍속도에 따른 영향은 거의 없는 것으로 나타났다. 또한 현재 국내의 쌀 등급 기준 중 싸라기율은 3% 이하를 1 등급으로 분류하고 있으며, 모든 실험조건에서 1 등급 기준을 충족하는 것으로 나타났다.
한편, 마찰식 정미기의 싸라기율은 일반적으로 3-5% 정 도이기 때문에 절삭식 정미기를 이용할 경우 도정수율 측 면에서 경제성이 높을 것으로 판단된다(Keum, 2008).
이와 같이 절삭식 정미기를 이용하여 현미를 가공할 경 우 싸라기율이 낮은 이유는 기존 마찰력과 찰리력을 이용 하여 백미를 가공하는 마찰식 정미기에 비해 절삭력을 이 용하여 비교적 낮은 압력에서 백미를 가공하기 때문에 싸 라기율이 낮은 것으로 판단된다.
절삭식 정미기의 절삭롤러 통풍구 수와 송풍속도에 따른 탁도 변화를 Fig. 6에 나타내었다. 탁도는 백미를 씻을 때 백미 표면에 붙어있는 미세한 쌀겨 및 성분 일부가 물에 씻겨 나오는 과정에서 발생하는 쌀뜨물의 탁한 정도이며, 일반적으로 백미의 탁도는 60-70 ppm 정도이다(KFRI, 2010).
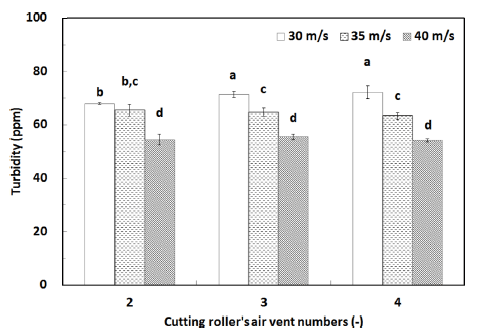
Fig. 6에서 알 수 있듯이 모든 조건에서 송풍속도가 증 가할수록 탁도는 감소하는 경향을 보였다.
정백 후 백미의 탁도는 절삭롤러 통풍구 수 2구의 경우 송풍속도 30, 35, 40 m/s에서 각각 68.0, 65.5 및 54.4 ppm 으로 나타났다. 또한 3구에서는 송풍속도 30 m/s 조건이 71.4 ppm, 송풍속도 35 m/s는 64.8 ppm, 40 m/s에서는 55.5 ppm으로 나타났다. 4구 조건의 경우 탁도는 송풍속도 30, 35, 40 m/s에 따라 각각 72.2, 63.3, 54.2 ppm으로 측정되 었다.
이와 같이 송풍속도가 빠를수록 탁도가 낮은 이유는 절 삭날에 의해 제거된 호분층이 강한 송풍에 의해 백미 표면 으로부터 분리가 원활하게 이루어졌기 때문으로 판단된다.
Fig. 7은 절삭식 정미기의 절삭롤러에 장착된 통풍 간극 링의 통풍구 수와 송풍속도에 따른 백미 1 ton을 생산하기 위한 에너지 소비량을 나타낸 것이다.
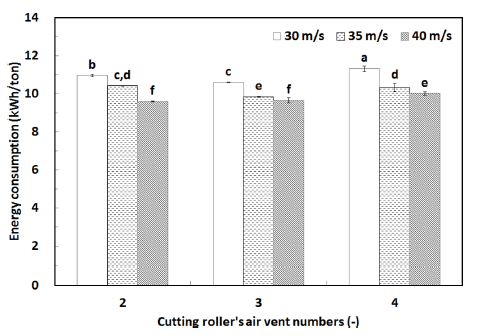
Fig. 7에 나타냈듯이 정백 중 에너지 소비량은 절삭롤러 통풍구 수 2구, 송풍속도 30, 35, 40 m/s의 조건에서 각각 10.96, 10.42, 9.60 kWh/ton으로 측정되었고, 30 m/s 조건보 다 35 및 40 m/s 조건이 각각 4.9, 12.4% 정도 에너지 소 비량이 절약되는 것으로 나타났다. 또한 통풍 간극링의 통 풍구 수 3구에서 에너지 소비량은 송풍속도 30, 35, 40 m/ s에 따라 각각 10.60, 9.84 및 9.65 kWh/ton으로 측정되었 으며, 4구 조건의 경우 송풍속도 30, 35, 40 m/s 조건에 따 라 각각 11.31, 10.31 및 10.01 kWh/ton으로 나타났다.
한편, 통풍구 수에 따른 에너지 소비량은 3구 조건이 비 교적 적은 것으로 나타났으며, 송풍속도가 증가할수록 에 너지 소비량이 감소하는 경향을 보였다.
이와 같이 송풍속도가 빠른 조건에서 에너지 소비량이 적은 이유는 강한 송풍작용으로 인하여 가공 중 정백실 내 에 부하가 적게 걸렸기 때문으로 판단된다. 또한 통풍구 수 3구 조건이 4구 조건과 비교하여 에너지 소비량이 적 게 측정된 것은 전술한 바와 같이 4구 조건의 경우 정백 실로 투입되는 송풍량이 많아 정백 중 배출 속도가 빨라지 면서 정백 압력이 감소한다. 이로 인하여 백도가 저하되므 로 백도 저하 방지를 위해 배출구 압력판에 가압을 하면 정백 부하가 커지면서 에너지 소비량이 증가하기 때문이다.
요 약
본 연구에서는 절삭식 정미기의 절삭롤러에 장착된 통풍 간극링의 통풍구 수와 정백 중 발생하는 미강제거에 필요 한 흡인 송풍속도가 정백특성에 미치는 영향을 구명하여 절삭식 정미기 개발의 기초자료를 제시하고자 하였다. 그 결과를 요약하면 다음과 같다.
백도는 모든 조건에서 38±0.5로 측정되어 균일하게 정백 된 것으로 나타났다. 정백 후 곡온 상승은 송풍속도가 증 가할수록 곡온 상승이 낮아지는 경향을 보였고, 절삭롤러 통풍구 수 3구, 송풍속도 35, 40 m/s 조건에서 각각 15.4°C 14.6°C로 나타났다. 동할미율은 절삭롤러 통풍구 수 3구, 송풍속도 35 m/s 조건에서 2.13%로 가장 낮게 측정되었다. 싸라기율은 모든 조건에서 0.762-0.869%로 낮은 범위를 보 였다. 백미 1 ton을 생산하기 위한 에너지 소비량은 송풍속 도가 증가할수록 감소하는 것으로 나타났다.
따라서 절삭식 정미기의 절삭롤러 통풍구 수와 미강제거 를 위한 흡인 송풍속도에 따른 적정 정백조건은 곡온, 동 할미율, 싸라기율의 품질적인 측면과 에너지 소비량 등을 고려할 경우 절삭롤러 통풍구 수 3구, 송풍속도 35 m/s 조 건이 적절한 것으로 판단된다.